Блог
Влияние распределения углерода на полиэтиленовые трубы
Краткое содержание
Трубы с неоднородным распределением углерода показали 80%-ое снижение удлинения, в сравнении с трубами с однородным распределением тех.углерода. Домены полимера с меньшим количеством сажи или вообще без нее (окна) показали расслоение с полимерной матрицей при растяжении материала, что в конечном итоге привело к разрушению гораздо быстрее ожидаемого.
Ключевые слова
- полиэтиленовая труба
- распределение технического углерода
- прочность при растяжении
- поверхность излома
Аннотация
В данной работе было исследовано влияние распределения технического углерода на ухудшение механических свойств полиэтилена высокой плотности в виде пластиковых труб, используемых в водопроводных системах.Полиэтиленовые трубы со схожими концентрациями технического углерода, но с его разным распределением производились с использованием промышленного оборудования для компаундирования и экструзии. Образцы для исследования готовились непосредственно из образцов экструдированных труб и растягивались до разрушения с различной скоростью деформации. Распределения технического углерода на объемных образцах и поверхностях разрушения исследовались с помощью стерео- и растровой электронной микроскопии (РEM).
Было обнаружено, что распределение технического углерода, поверхности изломов и характер разрушений в этих трубах существенно отличаются. Несмотря на то, что первоначальные параметры испытаний на разрыв были схожими, свойства образцов за пределами участка упругости значительно различались, резко снижаясь в зависимости от распределения сажи. Трубы с определенным уровнем неоднородности в распределении технического углерода показали пластические и хрупкие разрушения, тогда как гомогенизированный черный и натуральный полиэтилен (без технического углерода) показали только пластическое разрушение.
Введение
Полиэтилен был и является предпочтительным материалом для изготовления различных пластиковых труб благодаря его оптимальным краткосрочным и долгосрочным механическим свойствам, легкости переработки и свариваемости. Технический углерод остается идеальным и наиболее экономичным решением для предотвращения фотодеградации полиэтилена под воздействием УФ-излучения.
Эффективность углерода (CB) в отношении предотвращения фотодеструкции полиэтилена при солнечном свете зависит от типа тех. углерода, размера частиц, концентрации и дисперсии.
Недостаточная дисперсия и распределение углерода в полиэтиленовых трубах может произойти, если углерод и натуральный полиэтилен плохо смешаны. Это приводит к тому, что области с более низким содержанием углерода появляются светло-темные завихрения на изображениях с микроскопа; их обычно называют «окнами». Эти окна в основном являются результатом плохого смешивания тех. углерода и натурального полиэтилена на одношнековой линии для производства труб без надлежащей конструкции шнека и необходимых смесительных элементов.
Чтобы предотвратить проблему смешивания, ISO 4427-1 требует использования предварительно компаундированного полиэтилена черного цвета для производства пластиковых труб. Также сообщалось, что эти черно-белые завихрения меняют направление на стыке соединения и маскируют дефекты сварки если таковые имеются. В последнее время проводилось несколько исследований хрупкого разрушения сварного соединения полиэтиленовых труб с недостаточно гомогенизированным техническим углеродом. Роль диспергации углерода в формировании и распространении трещин в полиэтилене остается неизвестной.
В настоящее время большой интерес представляет четкое понимание влияния распределения тех. углерода на механические свойства полиэтиленовых труб и соединений. Информации на эту тему очень мало.
В этой статье мы стремимся показать, как распределение тех. углерода влияет на механические свойства полиэтиленовых труб, путем изготовления пластиковых труб с контролируемым распределением углерода, содержащих низкие, средние и высокие уровни окон, а также проведения испытаний на растяжение труб и анализа поверхностей разрушения этих образцов с помощью стерео- и растровой электронной микроскопии (РEM). В следующих статьях будем рассматриваться влияние негомогенизированного распределения технического углерода на целостность сварного шва и параметры трещинообразования полимерных труб.
Материалы и методы
Порошок полиэтилена высокой плотности был отобран из реактора полимеризации. Его смешали с антиоксидантами и мастербатчем тех.углерода (MB), содержащим 40% сажи и 60% полимера-носителя, для получения предварительно смешанного (готового) материала черного цвета с использованием смесителя непрерывного действия с противовращением (Kobe Steel, Япония). Тот же самый порошок также был смешан с антиоксидантами, но без MB – мастебатча тех.углерода, чтобы получить стабилизированное неокрашенное полиэтиленовое соединение (NPC - НПС). Трубы с внешним диаметром 110 мм и толщиной стенки 22 мм были изготовлены с помощью одношнекового экструдера с диаметром шнека 60 мм и отношением длины к диаметру (L / D) 33 (Reifenhäuser, Германия). Для формования трубы использовалась четырехканальная спиральная фильера (матрица) с точным контролем нагрева семи различных зон. Для изготовления эталонных труб без “окон” использовался черный предварительно смешанный или готовый компаунд (Образец 1). Смесь непигментированного полиэтиленового соединения (NPC) и мастербатча тех.углерода (CBMB) была приготовлена с помощью барабанного миксера. Затем смесь использовали для производства труб с различным распределением тех. углерода (образцы 2, 3 и 4) путем изменения производительности экструдера и сохранения всех остальных параметров постоянными.
Описание образцов труб приведено в таблицe 1
Температурный профиль цилиндра поддерживался постоянным, в то время как скорость шнека изменялась для получения разного времени пребывания и, следовательно, разных уровней распределения сажи. Содержание тех.углерода во всех образцах труб было проанализировано пиролизом в потоке азота в трубчатой печи при 600 ° C в соответствии с ASTM D1603. Коэффициент расхода (FRR) рассчитывался как отношение MFR 21 к MFR 5. Плотность образцов измеряли с помощью баланса (весов) плотности согласно ISO 1183-1, Метод A.
Таблица 1
Образец № | Описание | Материал | Примечание |
Образец 1 | контрольный образец HE3490LS | предварительно приготовлена смесь (соединение) | Скорость экструзии: 115 кг / ч, 100% |
Образец 2 | Высокий количество окон | NPC+ CBMB смесь: непигментированное полиэтиленовое соединение + мастербатч | Скорость экструзии: 115 кг / ч, 100% |
Образец 3 | Средний количество окон | NPC+ CBMB смесь | Скорость экструзии: 95 кг / ч, 80% |
Образец 4 | Низкое количество окон | NPC+ CBMB смесь | Скорость экструзии: 70 кг / ч, 60% |
Дисперсия тех.углерода и распределение на образцах труб были измерены для сечений толщиной 15 мм, которые были вырезаны перпендикулярно оси трубы (направление поперечного потока с использованием стереомикроскопа в режиме пропускающего света (передачи света) (Carl Zeiss, Германия). СЭМ-анализ (РЭМ анализ) был выполнен с помощью прибора FEI Quanta 250 FEG SEM.
ISO 527-2 Tип1B Образцы на растяжение были вырезаны непосредственно из образцов труб на фрезерном станке с ЧПУ (IPT, Германия) для испытаний на растяжение при скорости испытания 25 мм / мин и начальном расстоянии между захватом 115 мм согласно ISO 6259-3.
Другой набор образцов был вырезан соответствии со стандартом ISO 8286 Tип 3 для испытаний на высокоскоростное растяжение при 250 мм / мин с начальным расстоянием между захватами 40 мм. Для анализа поверхности разрушения были использованы образцы для испытаний на высокоскоростное растяжение.
Тесты на растяжение проводились на универсальной машине для испытаний на растяжение (Zwick, Германия), оснащенной тензодатчиком (датчиком нагрузки) 50 кН с механическим клиновым захватом. Для измерения номинальной деформации использовалось смещение крейцкопфа с точностью до 1 мм. Испытания на растяжение образцов труб повторяли не менее пяти раз. Все образцы кондиционировали при температуре 23 ° C и относительной влажности 50% в течение не менее 24 часов после подготовки образца.
Результаты
Содержание тех.углерода, MFR и плотность каждого образца представлены в таблице 2. Все трубы показали очень похожие значения. Однако содержание тех.углерода несколько отличалось для образцов 2–4 из-за процесса сухого перемешивания.
Таблица 2
Материалы | Содержание углерода %,вес | ПТР 5г/10мин | ПТР 21г/10мин | Коэффициент расхода 21/5 | Плотность г/см3 |
Предварительно компаундированный черный ПЭ | 2,11 | 0,27 | 8,76 | 32,4 | 0,96 |
неокрашенное полиэтиленовое соединение | не измеряется | 0,27 | 8,77 | 32,5 | 0,95 |
Образец 1 | 2,11 | 0,25 | 8,07 | 32,3 | 0,9603 |
Образец 2 | 2,26 | 0,27 | 8,09 | 30,0 | 0,9607 |
Образец 3 | 2,40 | 0,26 | 7,99 | 30,7 | 0,9606 |
Образец 4 | 2,37 | 0,28 | 8,26 | 29,5 | 0,9609 |
Дисперсия и распределение технического углерода в образцах, приготовленных из направлений поперечного потока, показаны на рисунке 1. Дисперсия тех. углерода во всех четырех образцах оказалась хорошей; то есть ни в одном из образцов не наблюдались агломераты тех. углерода размером > 30 микрон. Однако гомогенизация (смешивание) оказалась совсем другим.
В образце 1 не было окон, которые не содержали тех. углерод, хотя наблюдалось несколько пятен, которые не содержали углерод. Согласно ISO 18553, визуальная оценка внешнего вида образца 1 составляла A1 / A2, что находится в приемлемом диапазоне.
Образец 2 показал наихудший уровень гомогенизации среди четырех образцов. В этом образце был замечен высокий уровень окон. Ширина наиболее выступающих окон находилась в диапазоне 200–300 мм. Согласно ISO 18553 визуальная оценка его внешнего вида находилась между С1 и С2.
Образец 3 также показал высокий уровень окон; однако концентрация окон на единицу площади была немного ниже, и окна были тоньше по сравнению с образцом 2. Ширина наиболее заметных (выступающих) окон находилась в диапазоне 80–140 микрон. Визуальный рейтинг его внешнего вида был наиболее близок к С1.
В образце 4 было меньше окон, чем в образцах 2 и 3. Ширина наиболее заметных окон находилась в диапазоне 50–100 микрон. Визуальный рейтинг его внешнего вида находился между B и C1.
Рисунок 1
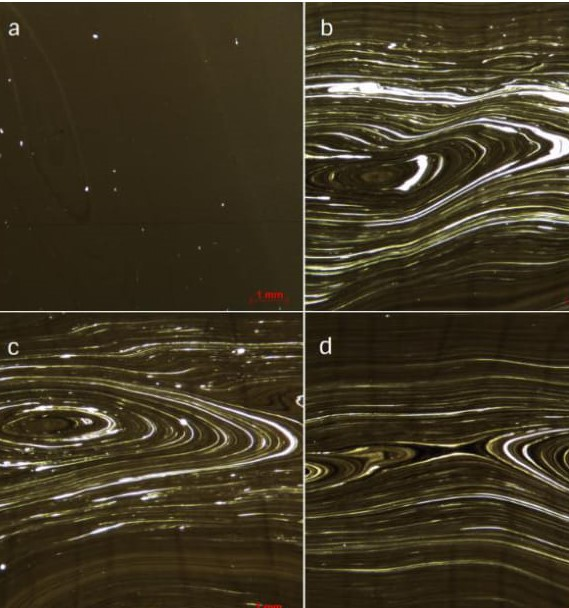
Испытания на растяжение образцов труб
Наложение инженерных кривых напряжение-деформация при 25 мм / мин (скорость деформации 13 с-1) для репрезентативных образцов каждого вида, приведено на рисунке 2. Образцы 1, 3 и 4 показали стандартное поведение кривой растяжения для материала полиэтилена высокой плотности: (а) упругая область (линейное увеличение напряжения с деформацией), (б) предел текучести (первое максимальное напряжение на кривой зависимости напряжения от деформации), (c) смягчение деформации (немедленное снижение напряжения), (d) естественная вытяжка (постоянное напряжение в зависимости от деформации), e) деформационное упрочнение (линейное увеличение напряжения за счет увеличения деформации) и, наконец, (f) разрушение образца.
Первоначальные параметры растяжения образцов приведены в таблице 3. Параметры предела текучести при растяжении образцов оказались аналогичными. Учитывая физические свойства образцов, приведенные в таблице 3, этого можно ожидать, поскольку свойства текучести при растяжении полиэтиленовых материалов зависят исключительно от плотности материала. С другой стороны, параметры за зоной упругости образцов при растяжении показали значительные различия.
Рисунок 2
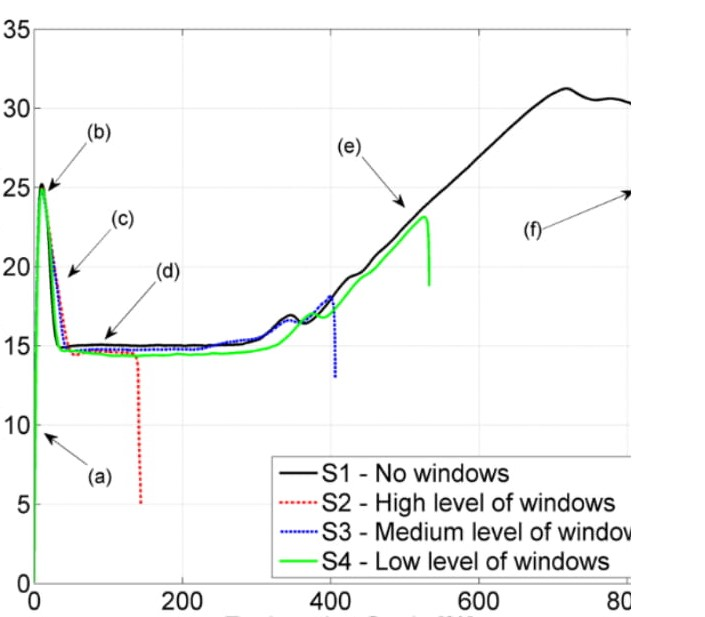
Таблица 3. Испытание на растяжение (25 мм / мин) образцов труб.
Образцы | Напряжение при пределе упругости MPa | Максимальная упругая деформация % | Предел прочности, MPa | Относительное удлинение при разрушении % |
S1 среднее/среднеквадратическое отклонение | 25,2 / 0,1 | 10 / 0,1 | 30,1 / 0,3 | 800 / 70 |
S2 среднее/среднеквадратическое отклонение | 25 / 0.5 | 10 / 0.1 | 15.6 / 2.5 | 270 / 160 |
S3 среднее/среднеквадратическое отклонение | 24.9 / 0.3 | 10 / 0.1 | 19.8 / 4.2 | 430 / 130 |
S4 среднее/среднеквадратическое отклонение | 24.9 / 0.3 | 10 / 0.1 | 25.7 / 6.3 | 670 / 220 |
Наблюдения в ходе экспериментов на растяжение показали, что образование вытянутой шейки в образце 1 происходит по всей длине. После стадии упругого удлинения, деформационного разупрочнения, общей текучести и деформационного упрочнения, когда толщина образца в зоне захвата уменьшилась до уровня, на котором механические захваты больше не могли удерживать образец, образец разрушился при 740% номинальной деформации без настоящего разрыва, но из-за выскальзывания из захватов. Этот показатель значительно превышает значение удлинения, требуемое ISO 4427-2, которое составляет минимум 350%.
Однако образец 2 с такими же молекулярными и физическими свойствами, что и образец 1, как указано в таблице 3, потерпел неудачу при значительно более низких деформациях, в среднем 270%, после того, как продемонстрировал значительно уменьшенное вытяжение без деформационного упрочнения.
Образцы 3 и 4 показали конечные параметры растяжения материала, которые были лучше, чем у образца 2, но хуже, чем у образца 1. В среднем образцы 3 и 4 соответствовали минимальному удлинению, требуемому ISO 4427-2, но по большому среднеквадратическому отклонению можно понять, что некоторые образцы показали удлинение менее 350%. Видимо, эти окна являются источником концентраций напряжений, особенно на их границах. В настоящем исследовании это явление наблюдается во время испытаний на растяжение.
На рисунке 3а перед испытанием показан образец для растяжения перед тестированием. Белые стрелки указывают окна, которые видны на поверхности образца. На рисунке 3b показан тот же образец с удлинением на 20% после деформации. На этом этапе многие другие окна стали видны невооруженным глазом из-за явления побеления от нагрузки. Границы окон, физические свойства которых неоднородны, по мере удлинения материала становятся более резкими (рис. 3c). В какой-то момент наблюдаются микротрещины на острых краях окон из-за плохого соединения границ раздела (рис. 3d) и более высокой концентрации напряжений. Эти микротрещины развивались с увеличением деформации и, наконец, привели к макроскопическому разрушению, как показано на рисунке 3e.
Рисунок 3
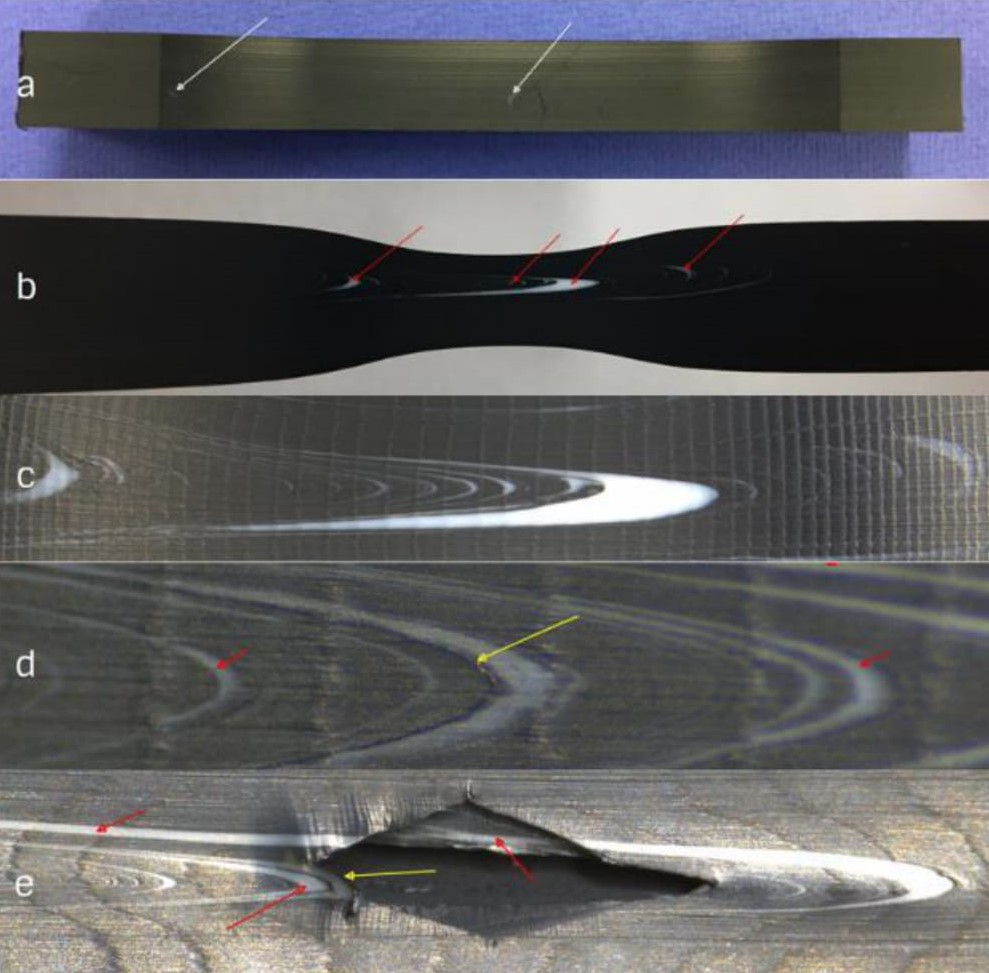
Анализы поверхностей разрушения
На рис. 4 представлены изображения поверхностей изломов всех образцов с помощью световой микроскопии при скорости перемещения (вытеснения) 250 мм / мин. Типичная поверхность разрушения полиэтилена при большом удлинении наблюдалась для Образца 1. Образец 3 и Образец 4 также показали поведение разрушения, подобное Образцу 1, причем Образец 3 показывает крошечные окна, видимые невооруженным глазом (Рисунок 4 (c), красные стрелки). Поверхности разрушения образцов показали, что точка концентрации собственных напряжений инициировала разрыв в средней части образца (Рисунок 4 (a), зона A) с последующим распространением через фибриллированные клинья (Рисунок 4 (a), зона B) до разрушения.
Образец 2 показывает полное хрупкое на макроскопическом уровне, связанное с негомогенной структурой матрицы из-за плохого перемешивания тех. углерода, что хорошо видно на рисунке 4 (b), на котором окна хорошо видны невооруженным глазом (красные стрелки). СЭМ-изображения черных областей (Изображения растровой электронной микроскопии черных областей) (рис. 5b) показали, что похожие уплотненные трещины развиваются до полного разрушения. СЭМ (растровая электронная микроскопия) поверхности излома Образца 2 в области с окнами (рис. 5а) показывает хрупкую природу разрушения, связанную с сильно фибриллированной структурой, которая аналогична тем, которые наблюдаются при медленном росте трещин в полиэтилене.
Рисунок 4
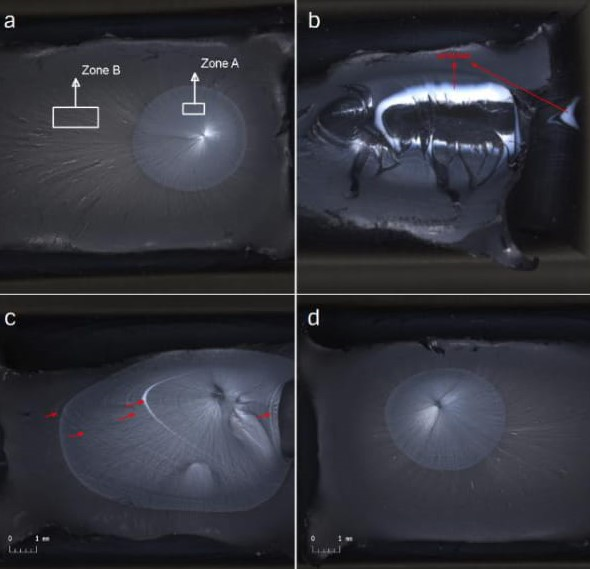
Рисунок 5
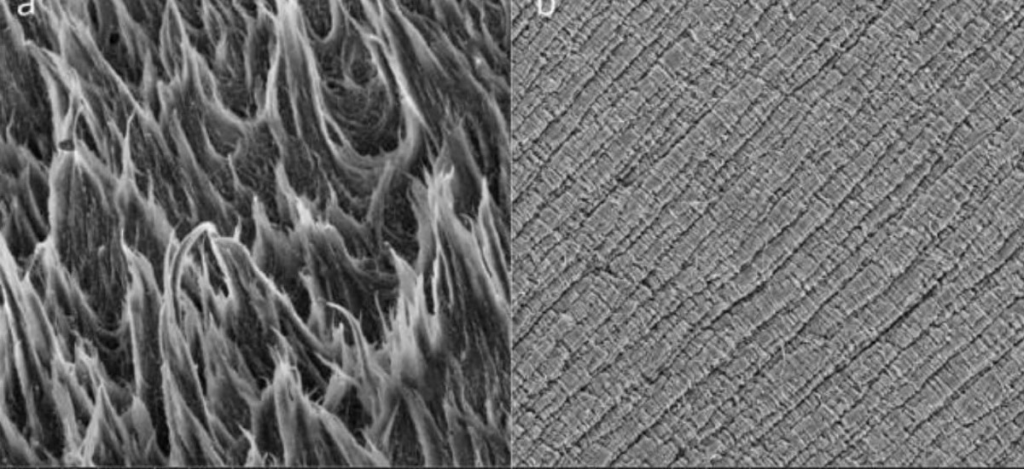
Выводы
В этом исследовании были изготовлены четыре пластиковые трубы из одного и того же полиэтиленового материала с различным распределением тех. углерода посредством одношнековой экструзии. Эти трубы были растянуты до разрушения посредством испытания на растяжение. Поверхности разрушения труб исследовали с помощью световой и растровой электронной микроскопии. Отмечено, что распределение тех.углерода при прямом добавлении мастербатча было неадекватным. Увеличение времени пребывания за счет снижения скорости производства помогло улучшить распределение углерода; однако даже при снижении производительности на 40%, распределение углерода в одностадийно компаундированных трубах не соответствовало уровню гомогенизации в трубах из предварительно приготовленного черного компаунда. Наблюдалось значительное снижение конечных параметров растяжения полиэтиленовых труб с недостаточным распределением углерода, в то время как первоначальные параметры растяжения не пострадали.
Трубы с добавлением концентрата сажи в процессе экструзии показали на 80% меньшее удлинение, чем трубы из предварительно приготовленного компаунда.
Домены полимера с меньшим количеством углерода (окон) или без них показали расслоение с полимерной матрицей по мере вытяжения материала, что в конечном итоге привело к разрушению намного раньше, чем ожидалось. На изломанных поверхностях труб, изготовленных одностадийным методом, наблюдалось крайне неоднородное распределение углерода. Интерес представляет тот факт, что полимерные домены без углерода в полимерной матрице демонстрируют хрупкое разрушение, хотя соответствующий неокрашенный материал демонстрирует полностью пластичное разрушение, когда он испытывается как отдельный образец. Наконец, мы сообщили о значении однородности углерода для механических свойств пластиковых труб. Это же касается и фитингов. Для инженеров-конструкторов также представляет большой интерес понимание целостности сварных швов пластиковых труб. Поэтому в следующей статье будет сообщено о влиянии распределения углерода на механическую целостность сварных соединений полиэтилена.